Wire forms are everywhere and are used in nearly every industry and business sector. But what are wire forms and how are they made? In this article, we tell you everything you need to know about wire forms for your next application.
In Need of Wire Forms?
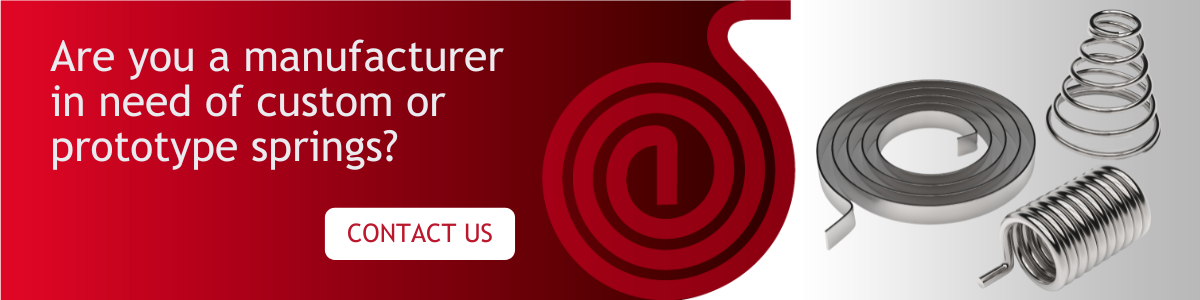
What Are Wire Forms?
At the most basic level, a wire form is a length of wire that has been formed into a specific shape for a specific purpose. Wire forms come in endless configurations and can be customized for just about any purpose. A wire form can be bent, cut straight or with angles, wound right or left, shaped with closed coils, can have additional pieces added to it, and just about anything that a customer can think of. Springs are an elaborate type of wire form.
Industries That Use Wire Forms
Because of the versatility of wire forms, it is not an exaggeration to say that they can be found, in one form or another, in almost every industry, including:
- Aerospace
- Agricultural
- Athletics
- Automotive
- Construction
- Electronics
- HVAC
- Medical Devices
- Injection Molding
- Petroleum
- Pharmaceuticals
- Retail
Common Wire Form Applications
Wire forms are used in endless applications including door strikers, exhaust hangers, hood prop rods, and instrument panel supports to name a few. Here are other common applications.
- Spring Hinges
- Battery Contacts
- Mousetraps
- Safety pins
- Large Wire Applications
- Electrical Applications
- Lightbulb filaments,
- Musical instruments
- Clocks
- Pins
- Pegs
- Rivets
Types of Wire Forms
Wire forms can take nearly any form and be used for many purposes. Here are common wire form types and uses.
- Springs. Of all the types of wire forms, springs are the most common and widely used. They are a coil that has been wound into a tightly wrapped spiral to meet preset force or torque requirements.
- Linchpins. Linchpins are inserted into the end of an axle to prevent wheels from coming off. They are made from aluminum, zinc, brass, and stainless steel.
- Utility Hooks. Utility hooks have a threaded end and hook, which allows for easy installation. A utility hook requires multiple bends during the manufacturing process including an offset bend to both sides of the loop with a bend at the end of the loop that touches the other side.
- S Hooks: Both ends of an S hook are bent to form the S shape. They are normally used for hanging storage or for organizing cables, hoses, and cords as a safety measure.
- J Hooks. There are many varieties of J hooks with the most common being the fishhook. They can be coated for protection of materials placed on them and have notches so they can be hung. Double J hooks are capable of holding huge loads when attached to a strap.
- Wire Displays. Wire displays are a durable and inexpensive means for displaying products. They are produced by bending, shaping, and forming wire made of low, medium, or high carbon steel but can also be made of stainless steel, copper, and aluminum brass. Once they are wire-formed, they can be coated, plated, or painted.
- Wire Baskets. Wire Baskets are used for bulk storage of parts, equipment, and components. They are made of a welded wire mesh. Some forms have a rust-resistant electro galvanized finish to prevent wear and rusting. The open mesh design provides excellent strength, inventory control, visibility, and forklift access. In production facilities, they can be used to strategically place parts for easy access.
- Wire Guards. Wire guards are designed to prevent access to equipment, passageways, instruments, and sensitive materials. Hinged wire guards, or wire cages, are used to protect sensitive equipment in high traffic areas from the activities associated with manufacturing locations and athletic fields. Open face wire guards prevent activation of fire alarms or emergency stop switches.
- Z Clips. Z clips are used to lock components in place. The long portion of the Z clip slips over the item to be held and is anchored at both ends to form a secure hold. They come in a wide range of thicknesses and diameters depending on how they are used. The benefits of Z clips are their strength, versatility, and resistance to corrosion.
- Threaded Wire Forms: In the wire form threading process, a metal rod is rolled through a set of threading dies that create the peaks and valleys of the threads. Unlike the rolled threading process, cut threading removes metal from the workpiece to create the threads and can be used with a wider range of diameters, thread lengths, and pitch combinations.
- Hose Clamps: Wire hose clamps use heavy wire that is bent into a U shape, which is formed into a ring with one end of the wire overlapping the other end. The two ends are bent upward so they can be opened. When the bent ends are pushed apart, they tighten around the hose and provide equal pressure to seal off the hose from leaks.
- R Clips: R-clips are fasteners made of metal wire shaped into the letter R. They have a similar use to that of a linchpin and are used to secure the end of an axle or rod with a wheel. The long straight portion of the clip fits through a hole at the end of the shaft, while the springy part goes over the shaft at the top or bottom.
Why Choose Spring Dynamics for Your Wire Forms
Spring Dynamics manufactures wire forms for many industries and applications. Our state-of-the-art machinery handles complex designs and we are able to run both small and large quantities.
Your product development team is welcome to work with our engineering group to identify which wire form will work best for your application. You might be surprised — in many cases, we are able to suggest advantages not previously considered.
- We can produce a variety of wire sizes and styles, from round to rectangular.
- We work with a variety of materials – copper, stainless, cold-rolled steel, soft bronze, coated materials, and many other exotic materials
- Quick turnaround times
- Custom design and production services
- Prototype capabilities for short-run evaluation tests
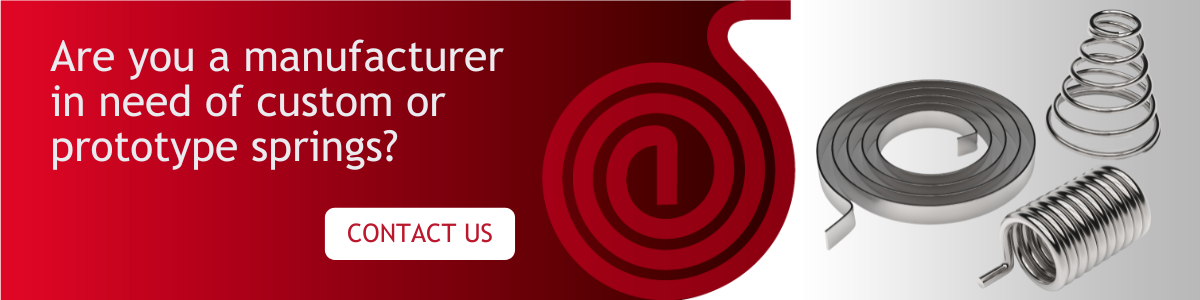